REDUCE WAITING TIME.
INCREASE YOUR PRODUCTIVITY.
It is essential that we know that throughout the fusion process, the time we use for each joint is directly linked to the cooling procedures. When we meet the times described in the ASTM standards we will be decreasing the overall productivity of the workplace. Therefore, the most practical method of optimizing the fusion process is to reduce this cooling time.
Our Datalogger uses an own cooling algorithm with which it is calculated in real time, those times that are most effective always depending on the materials we are using, environmental conditions and thermal immersion time. This algorithm is a formula (patent pending) that indicates the exact times it takes to cool the center of a pipe, making the handling safe and so you can move on to the next joint.
SOME EXAMPLES OF THE TIME YOU WILL SAVE BY THE OPTIMIZED MCELROY COOLING PROCEDURES
20″, DR11 PIPE AT 75°F





55%
REDUCTION IN COOLING TIME





39%
REDUCTION IN OVERALL TIME TO COMPLETE A JOINT
MCELROY OPTIMIZED COOLING IS F2620 COMPLIANT
For some time, McElroy experts have partnered with the University of Tulsa in the United States to perform thousands of tests and analysis of fusion joints. These tests analyze thousands of data points and the modeling of computational fluid dynamics in order to better understand the temperatures of the center of the pipes. Thus, we are totally convinced that McElroy’s optimized cooling system complies with ASTM F2620-19, Note 10. It was with this series of tests that McElroy managed to create his algorithm, which predicts time safely, and accurately for the core cooling of a pipe wall with a joint resistance expected at that time and temperature. This translates into a much safer handling and work for all operators.
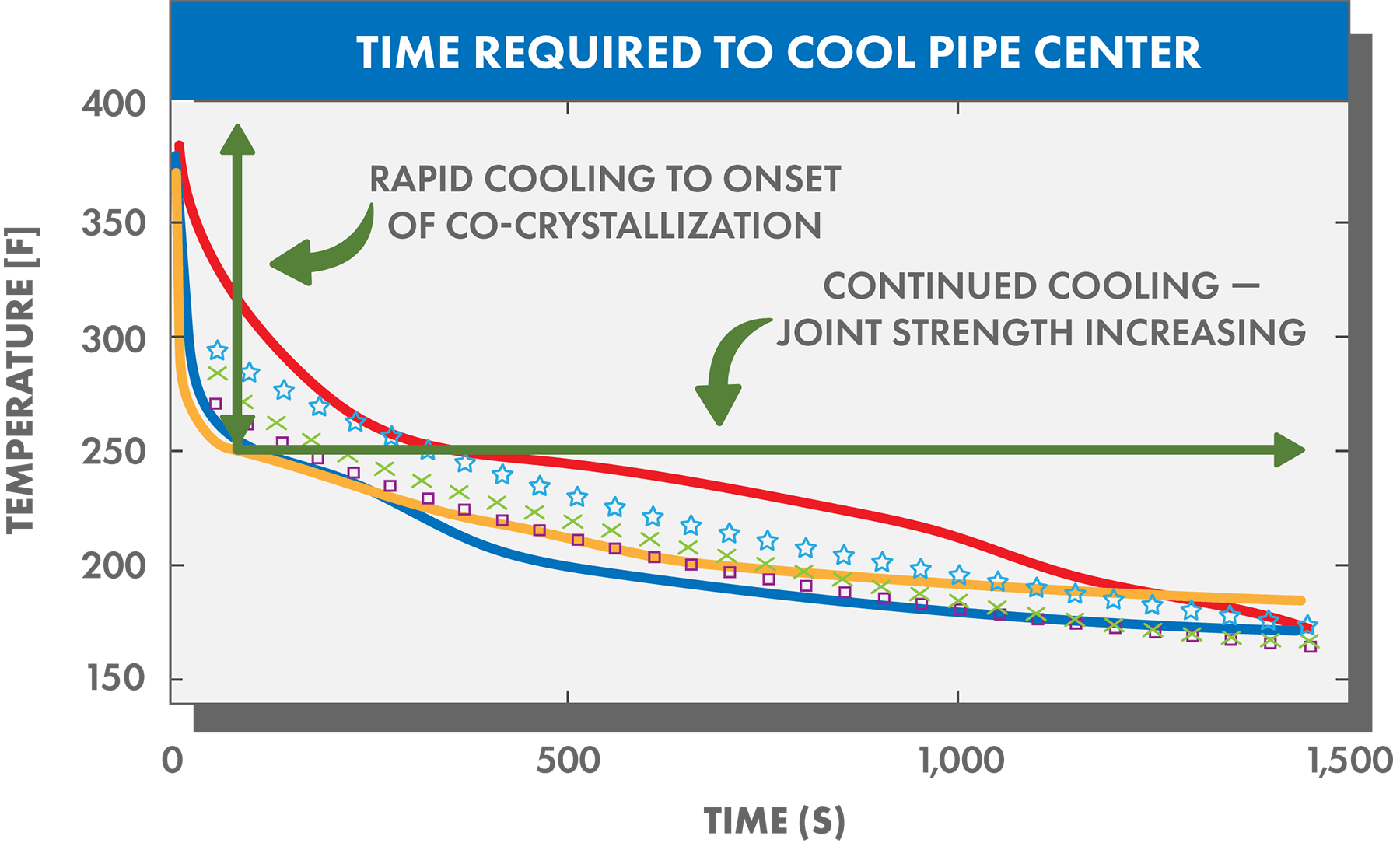
PRESENTED AT
Presented at McElroy INFUSION18, Plastic Pipes XIX, Plastic Pipes Sydney and INFUSION19.
Deja tu comentario